key competence
composite materials
Our competence center meets the challenges of industrial competitiveness to develop lighter aeronautical and spatial structures that are both resistant and multifunctional, by using high-performance composite materials.
We focus on the development of materials from thermostable organic matrices (PEEK, PEKK, PAEK, and high-temperature polymers), to thermoplastics or thermosets and ceramic matrices resistant at very high temperatures (aluminum oxide Al2O3, silicon carbide, vitroceramics, etc.). The applications targeted are the critical mechanical structures of aircraft, launchers, satellites, and motors whose reliability has to be guaranteed.
We design and develop new multifunctional composite materials with managed architectures, and we also operate on a semi-industrial scale. Going beyond the technological error testing approach often found in industry, we develop digital tools and methodologies to design and manufacture high value-added materials and structures.
This enables, for instance, to reduce design and qualification phases for industrial understanding (virtual testing) of the influence of setting parameters of development means on the microstructure and properties of materials (virtual manufacturing).
Eventually, we also help technicians, engineers, and PhDs to develop their skills, and train PhD students for careers in the formulation and implementation of new generation high-performance composites.
R&T fields
MULTIFUNCTIONAL MATERIALS
The functionalization of composite materials is a major scientific and technological challenge to exploit the performance of these much-researched materials.
The research deals with:
- the formulation and the deposition of fiber sizing adapted to matrices;
- the elaboration of high-temperature prepregs*;
- the definition and the implementation of methodologies and processes to functionalize the raw material or the prepreg (in bulk or on the surface, ex: electrical conductivity, thermal conductivity, damping properties, acoustic noise reduction, etc.).
*A prepreg is a semi-product formed of a matrix impregnating a reinforcement that ensures high breaking strength. The matrix may be thermoset or thermoplastic resins impregnated with reinforcement fibers (glass fibers, fabric, biosourced or recycled fibers, carbon fibers). This highly charged composite is earmarked for hot molding under pressure to manufacture a finished product. In the case of CMC, the matrix is a ceramic powder reinforced by ceramic or carbon fibers. This composite highly charged with ceramic particles of low grain size is then consolidated at a very high temperature (>1000°C) to manufacture a finished product.
MANUFACTURE NEW PREPREG AND MANAGE ITS ARCHITECTURE TO INCREASE ITS PROCESSABILITY AND COST COMPETITIVENESS
Very large savings can be expected by abandoning the consolidation in autoclaves. Prepregs must be adapted to these new processes. Our research focuses on understanding the relations between the prepreg architecture and the evacuation of porosities through the different process stages and the final properties of the laminates.
The architecture of prepregs is optimized experimentally and by modeling critical stages in the elaboration process. Our final objective is to define the optimized micro-structure tapes for a given final consolidation process and to demonstrate the industrial capability to produce them.
INDUCTION WELDING PROCESSES
How well thermoplastics can be welded is a major source of increased competitiveness during the assembly process. This is why we study continuous and dynamic direct welding processes of stratified materials to unidirectional carbon fibers. Through this process, we use strong multi-physical coupling between magnetic, electrical, thermal, physical, and mechanical aspects. Based on a simultaneous approach of test-modeling, it is primordial to understand these interactions to take the technology to the maturity level required for future generation single-aisle aircraft.
Our competence to functionalize composite, i.e to integrate tailored properties added to adapt material behavior during the welding process, is also a significant enabler to optimize the welding processes.
VIRTUAL MATERIAL, MANUFACTURING, AND TESTING
Simulation tools help to significantly reduce the development and qualification time of composite parts. Our core research in modeling and simulation deals with three thematics:
- Multiphysics and multiscale modeling (virtual testing at multiple scales -material, coupon, structure- homogenization & multiscale analysis, modeling manufacturing process & defects);
- Smarter testing and advanced characterization (reducing testing samples with instrumentation -DIC, in-situ, etc.- developing specific tests to calibrate advanced material model, augmented simulation, model-based characterizations);
- Integrated Computational Materials Engineering (deterministic and probabilistic predictions, design and manufacturing process optimization, data analysis/data-driven modeling, machine learning and AI-based models, verification and validation process, etc.).
We can name two overall objectives for this R&T field: to predict the behavior of increasingly complex testing pieces by using data from materials (such as variability, statistic dispersion…) and to provide efficient decision-making support tools for aircraft manufacturers’ design industry, while allowing substantial savings in time during the design phase and costs, due to the qualification/certification of materials and structures.
INNOVATIVE CERAMIC COMPOSITE MATERIAL AND PROCESSES
Here the objective is to support the development of carbide and oxide ceramic matrix composites (CMCs), as well as the maturing of processes to produce internal or exhaustive parts for aircraft engines (large-scale production at low cost).
On one hand, research on SiC CMC focuses on the processes of texture treatment, impregnation, slurry injection, and siliconizing, as well as bringing to maturity the appropriate testing technologies.
On another hand, research on oxide-oxide CMCs aims at showing the feasibility of dry or wet impregnation of an oxide thread compatible with manual or automated fiber placement. Modeling is included in our development mainly for conception. Non-destructive methods are implemented as soon as they are justified. CMC activities develop solutions for aircraft, space, defense, and energy applications.
Our offer
- State-of-the-art, technical syntheses, technological and scientific watch
- Design and manufacture at the semi-industrial scale of multifunctional organic and ceramic composites
- Complete multiscale characterization of composite materials and structures
- Databases on materials and behavior models
- Customized and digital decision-making support tools for design office or key process parameters optimization
ROADMAP
2020 > 2025
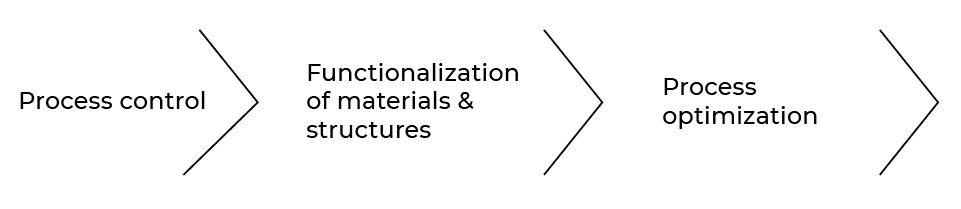
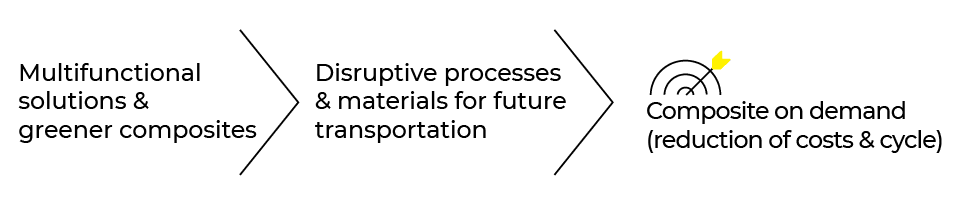
contact us
Contact our platform experts team
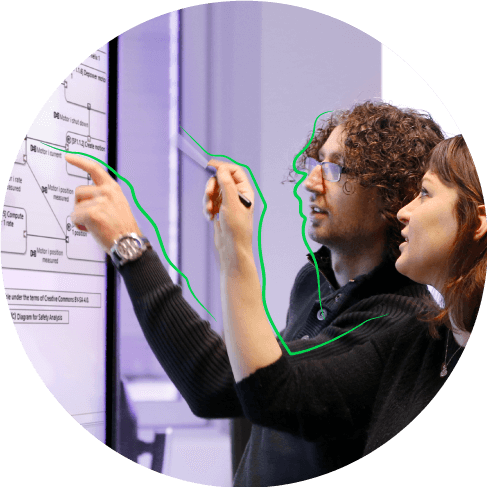