Fidèle à ses efforts de recherche et d’innovation en technologies de fabrication additive métallique, l’IRT Saint Exupéry fait évoluer ses outils et son offre de service en dotant son équipement de Compaction Isostatique à Chaud (CIC) d’un analyseur de gaz.
Cette modification est réalisée dans le cadre du projet HIPPOME ayant comme membres Safran, Air Liquide, Le Laboratoire CIRIMAT en tant que membre académique, et Quintus en tant que partenaire collaboratif. Cet analyseur permet de mesurer des concentrations d’impuretés, tel que l’oxygène, l’hydrogène, l’azote, la vapeur d’eau et le méthane, jusqu’à des niveaux de l’ordre de la centaine de ppb (partie par milliard). Ces mesures précises de l’atmosphère de traitement permettront d’améliorer l’état de surface des pièces après un cycle CIC.
Le projet HIPPOME
Le projet HIPPOME a pour objet principal l’étude des phénomènes d’oxydation durant un traitement thermique de type CIC d’un superalliage à base de nickel mis en forme par fabrication additive LBM (Laser Beam Melting) ou par le procédé MIM (Metal Injection Moulding). De plus, ce projet comprend une activité sur le développement de nouvelles gammes de traitement thermique en intégrant le CIC comme moyen de mise en place de la microstructure.
Depuis mai 2021 l’IRT Saint Exupéry relève les défis au fil de l’avancement du projet HIPPOME et fait face à des challenges liés à l’état de surface des pièces élaborées en fabrication additive métallique en sortie du processus de Compaction Isostatique à Chaud (CIC). Nos collaborateurs, Jonathan Hugues, Nicolas Mrozowski, Aurélien Prillieux, Thibaut Mancier, Mauro Ravaioli et Simon Pérusin mènent les recherches visant à améliorer cette étape de post traitement pour pouvoir garantir un meilleur état de surface en sorti de traitement thermique et la fiabilité des matériaux.
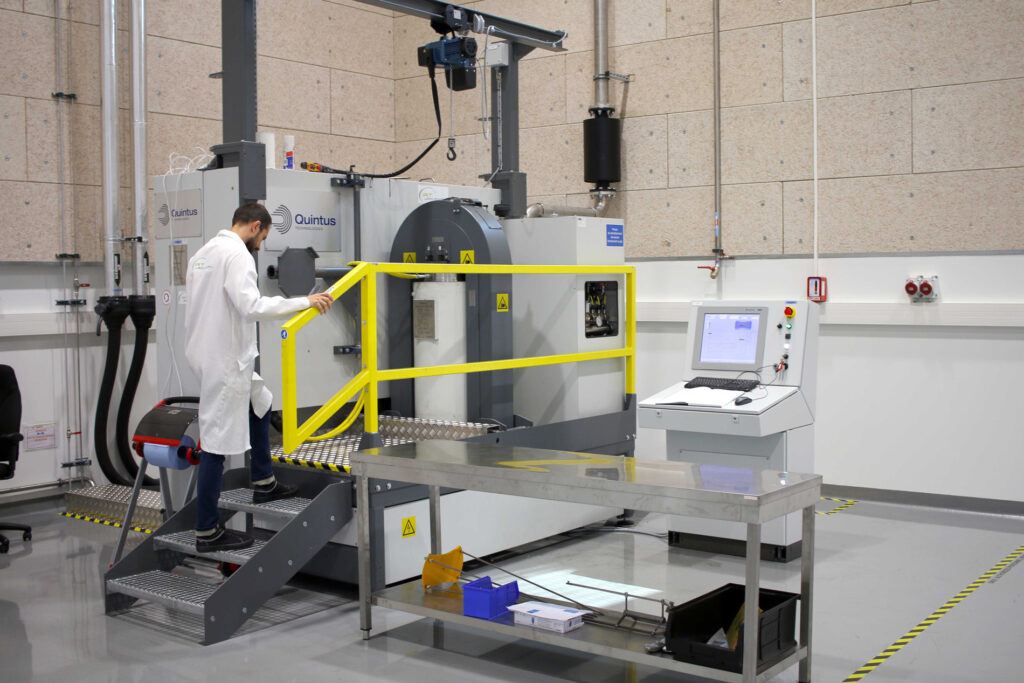
Le processus de CIC applique de fortes pressions et températures sur la matière pour enéliminer les défauts en sortie de fabrication additive et s’assurer qu’elle soit parfaitement dense. Cette étape permet d’améliorer le comportement des pièces en utilisation réelle, notamment lors de sollicitations mécaniques de type fatigue.
Bien qu’un gaz protecteur, ici de l’argon, soit utilisé lors du traitement, au terme de cette étape, les surfaces des pièces traitées présentent une couleur noire, liée aux réactions entre les impuretés contenues dans l’atmosphère du CIC et la pièce. Ces états de surface dégradés sont néfastes pour d’autres procédés d’assemblage en aval notamment pour certaines pièces non usinées, pièces dites « Near net shape ».
Pour prévenir ces phénomènes de contamination, il est nécessaire de comprendre quelles impuretés dans le CIC réagissent avec les pièces qui y sont placées : oxygène, vapeur d’eau, azote, carbone ? C’est ici que l’analyseur de gaz adjoint au CIC entre en jeu
L’IRT est accompagné sur ce projet par Quintus, (fabricant d’enceinte de CIC), pour la création d’un point de piquage permettant de prélever le gaz à analyser au plus près des pièces traitées, et par Ldtek, marque du Groupe Process Sensing Technologies et fabricant de l’analyseur de gaz, et Air Liquide, pour son installation et son étalonnage.
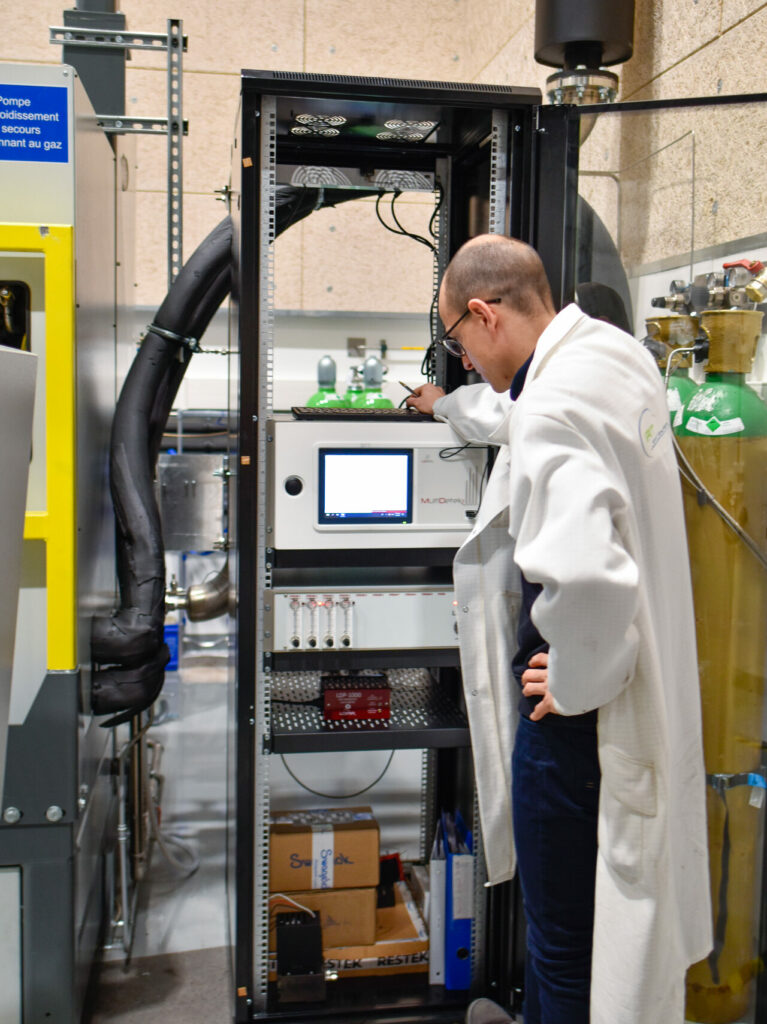
Une capacité à prélever du gaz sur ce type d’équipement unique en Europe
Le système de piquage développé par Quintus va permettre de prélever du gaz à haute température et à haute pression (jusqu’à 1400°C et 2000 bar) dans la zone de traitement des pièces. Ce gaz est ensuite envoyé vers l’analyseur pour en déterminer la composition et ainsi identifier précisément les réactions entre les impuretés du gaz et les pièces en traitement. Cette capacité à prélever du gaz au plus proche des pièces et à pouvoir l’analyser est à l’heure actuelle unique en Europe sur ce type d’équipement.
Les résultats des analyses sont par la suite utilisés pour alimenter des calculs thermodynamiques Et ainsi prédire la formation potentielle de phase telle que des oxydes à la surface des pièces traités. Ces calculs permettent de comprendre l’évolution des surfaces des pièces lors du traitement et aident à développer la meilleure solution technologique pour améliorer leur état à la fin du traitement.
Au-delà de ces études, l’analyseur sert aussi aux industriels utilisateurs de ce type de moyen à améliorer leurs procédés. Quantifier des éléments contaminants dont les effets sont déterminés comme acceptables en dessous d’un certain seuil, permettra de valider les processus et d’être gage de qualité. Le CIC ainsi équipé permet désormais à l’IRT Saint Exupéry l’élaboration de cahiers des charges et de procédés pour obtenir des pièces de qualité optimale en minimisant le nombre d’étapes de traitement thermique.
Nos plateformes technologiques permettent de réaliser des travaux de recherche sur mesure, en respectant les besoins spécifiques de chaque client. Nous nous adaptons aux attentes de chaque client, au niveau de maturité de sa technologie mais aussi à sa taille, permettant ainsi aux start-ups, TPE et PME d’accéder à des ressources de développement uniques.
Informations clés
- Membres du projet : Safran, Air Liquide, laboratoire CIRIMAT, IRT Saint Exupéry et Quintus en tant que partenaire collaboratif.
- Cet analyseur est disponible dans le cadre de prestation de service et de projets de recherche.
- Il s’agit d’un équipement de pointe qui permet de détecter jusqu’à des teneurs de 100 ppb pour O2, N2, H2, CH4 et H2O.
- Permet de prélever du gaz dans un environnement soumis jusqu’à 1400°Cet 2000 bar de pression.
- L’analyseur offre des temps de réponse rapides et permet un suivi en continu pour l’oxygène et la vapeur d’eau grâce à des systèmes de mesure n’utilisant pas la chromatographie L’équipement permet également d’obtenir un point toutes les 200 s par chromatographie pour les espèces H2, N2 et CH4.