On April 21st, 2022, IRT Saint Exupéry held a press conference on the MAMA project (Metallic Advanced Materials for Aeronautics). During this occasion, IRT Saint Exupéry and the members of the project had the occasion to share and discuss about the technological and scientific advances of a project that will contribute to the reinforcement and the modernization of the French industrial sector of the aeronautical construction and its supply chain.
Nadia Pellefigue (Vice President in charge of International and European Relations, Higher Education and Research of the Occitanie Region), Damien Proust (VP Ho Airframe Propulsion Engineering at Airbus), Pierre Rega (Deputy General Manager of die-forged parts at Aubert & Duval), Jean-Marc Gomez (President of Mecaprec), Nicolas Pobeau (President of Recaero), Simon Pérusin (Head of the Metallic Materials & Processes Center of Competence at IRT Saint Exupéry) and Denis Descheemaeker (CEO of IRT Saint Exupéry) took the floor to present these major advances for the sector.
THE PROJECT
“The industrial objectives are to significantly reduce recurring manufacturing costs, reduce the volume of raw materials used, and develop solutions for repairing aeronautical parts with very high added value. The project also contributes to a significant reduction in the environmental footprint of the aircraft manufacturing industry.“
The project
Starting in 2018, the IRT Saint Exupéry carries out the MAMA project which aims to reduce the manufacturing costs of primary aerostructure parts and strengthen the economic competitiveness of the French industry in the field of aeronautical construction.
Among the results presented, an 800 mm long titanium Ti64 demonstrator corresponding to a scale 1:1 section of an Airbus A350 fuselage frame was unveiled. It demonstrated a reduction of more than 30% in the amount of raw material used in closed die-forging compared with the current industrial solution.
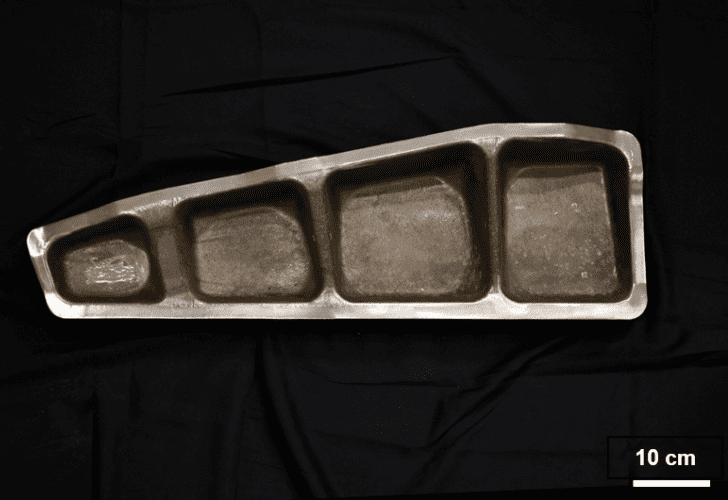
A SET OF TECHNOLOGICAL INNOVATIONS AT THE SERVICE OF AERONAUTICAL CONSTRUCTION
“The MAMA project team has been engaged in the search for technological levers to significantly reduce (30 to 40%) the quantities of raw material and energy consumed over the entire manufacturing range of elementary aeronautical parts made of Titanium Ti64 alloy.“
The objectives
This project aims to propose new conditions for closed die-forging/patterning aeronautical parts made of Titanium alloy (Ti64) and to combine them with emerging techniques of additive manufacturing by depositing powders and metallic wires.
All the scientific advances rely on a unique research platform in Europe developed during the project and dedicated to the hybridization between die-forging processes and metal additive manufacturing technologies.

The industrial objectives are to significantly reduce recurring manufacturing costs, reduce the volume of raw materials used, and develop solutions for repairing aeronautical parts with very high added value.
The project also contributes to a significant reduction in the environmental footprint of the aircraft manufacturing industry. It will end in the summer of 2023.
Technological fields
Since 2018, the MAMA project team has been engaged in the search for technological levers to significantly reduce (30 to 40%) the quantities of raw material and energy consumed over the entire manufacturing range of elementary aeronautical parts made of Titanium Ti64 alloy. Three avenues were identified very early in the project and led to a sustained research effort that is still ongoing:
- High-temperature die-forging to facilitate the flow of metal during shaping, a reduction in die-forging effort, and the production of a rough forged part (blank) closer to the desired final dimensions.
Obtaining such a blank, although it offers the advantage of significantly reducing the volume of material eliminated by the subsequent machining operations (milling), makes the latter very delicate. Indeed, given the very strong reduction of the excess thicknesses between the blank part and the finished part, the control of the deformations generated during these operations is a subject of the first order to guarantee in fine the dimensional tolerances of the machined elementary parts and their later assembly.
This control requires the implementation of simulation tools, validated by an experimental approach, which allows the identification of the most relevant machining strategies.
- The combination or hybridization of closed die-forging with additive manufacturing technologies to improve the technical and economic performance of closed die-forging. The operation consists of “depositing” material locally using an additive process on a blank from closed die-forging, to reconstitute a single part.
This combination of processes allows for an overall reduction in the amount of raw material used as well as in the pressing effort required for the forged part of the blank.
- Simplification of the semi-finished product manufacturing process. The semi-finished product or slug is the material used during the die-forging process. It is generally in the form of cylinders from forged bars.
The (open) die-forging operations, carried out at around 1,000°C for the Ti64 Titanium alloy, are very costly and energy-consuming. The work carried out within the framework of the project consists in revisiting these operations and simplifying them.
The developments carried out within the framework of the first two parts above have led to the identification of potential industrial outlets for additive manufacturing processes in the field of tooling and aircraft parts repair as well as in the spare parts market. This has led to an extension of the research work program in 2020.
Download our MAMA press kit (FR)
KEY INFORMATION
Key numbers
Duration of the project: 5 years (August 2018 – July 2023)
Budget: 10.4M € (partially financed by the PIA and the Occitanie Region)
Members: 11
Industrial members
Airbus, Aubert & Duval, IRT Saint Exupéry, Mecaprec, OPT’ALM, Recaero, Sciaky