MAMA Project
The MAMA project, led by IRT Saint Exupéry, aims to reduce the manufacturing costs of primary titanium aerostructure parts and boost the economic competitiveness of the French aeronautics industry
The industrial objectives are to significantly reduce recurring manufacturing costs, reduce the volume of raw materials used, and develop solutions for repairing aeronautical parts with very high added value. The project also contributes to a significant reduction in the environmental footprint of the aircraft manufacturing industry.
about the project
MAMA project research fields
to reduce the cost of titanium aeronautical structural parts
The project targets complex titanium aerostructure parts, enabling them to be closed-die-forged as close as possible to the finish machined shape. Current closed-die-forging technology, already used on many aircraft parts, produces parts with minimum wall thicknesses of 25 to 30 mm. Research results from the MAMA project have made it possible to achieve wall thicknesses of 15 mm.
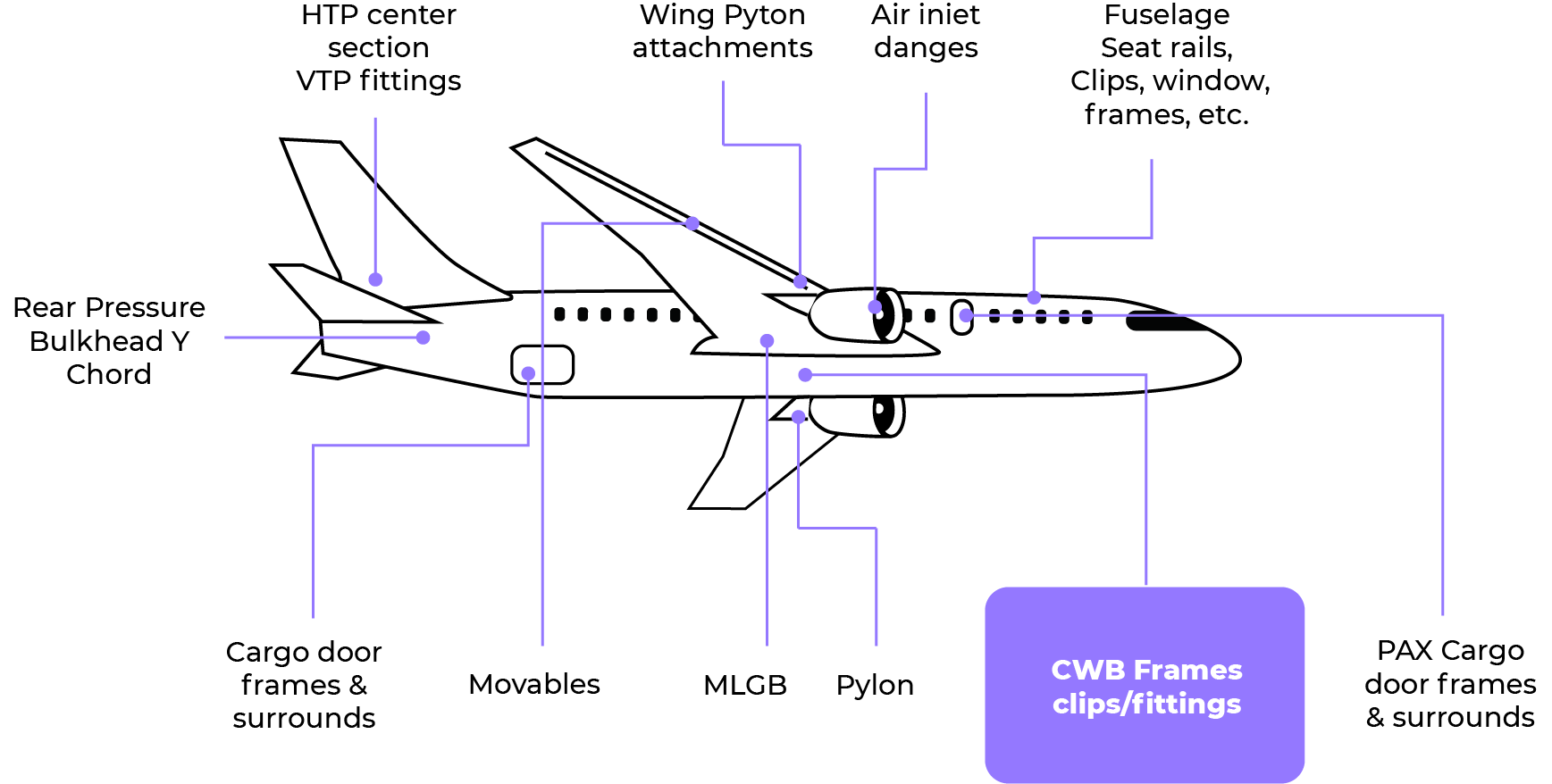
Figure 1 - Complex titanium aerostructure parts project targets
The semi-industrial scale at which the project's research work was carried out, the digital tools developed and the levels of maturity reached have enabled us to achieve savings of around 30% on the raw materials used, compared with the current industrial situation. These gains have been consolidated thanks to the strong involvement of the industrial and academic project members (aircraft manufacturers, titanium suppliers, forgings suppliers, machinists).
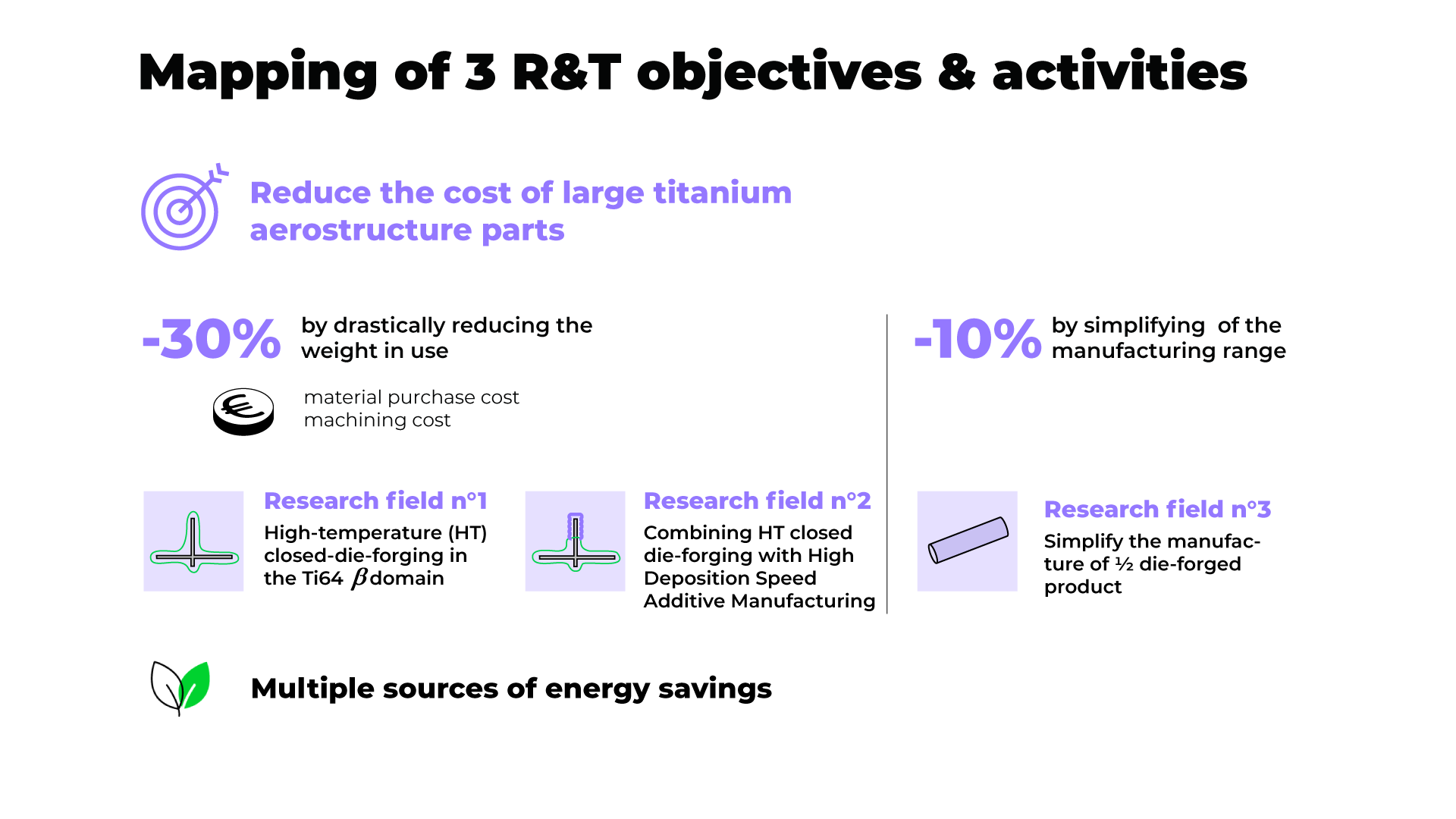
Figure 2 - Synthesis of the 1st three batches of the MAMA project to reduce Titanium raw material by 40%.
Objectives
MAMA project
Since 2018, the MAMA project team has been engaged in the search for technological levers to significantly reduce (30 %) the quantities of raw material and energy consumed over the entire manufacturing process of elementary aeronautical parts made of Titanium Ti64 alloy. Three avenues were identified very early in the project and led to a sustained research effort that is still ongoing:
- High-temperature closed-die forging to facilitate the flow of metal during shaping, a reduction in forging load, and the production of a rough forged part (blank) closer to the desired final dimensions.
Obtaining such a blank, although it offers the advantage of significantly reducing the volume of material eliminated by the subsequent machining operations (milling), makes the latter very delicate. Indeed, given the very strong reduction of the excess thicknesses between the forged blank and the finished part, the control of the deformations generated during machining is critical to the final dimensions of the component and its assembly into the aircraft.
This control requires the implementation of simulation tools, validated by an experimental approach, which allows the identification of the most relevant machining strategies.
- The combination or hybridization of closed die-forging with additive manufacturing technologies to improve the technical and economic performance of closed die-forging.
The operation consists of “depositing” material locally using an additive process on a blank from closed die-forging, to build a one-piece part. This combination of processes allows for an overall reduction in the amount of raw material used as well as in the forging load.
- Simplification of the semi-finished product manufacturing process. The semi-finished product or forged billet is the material fed to the closed-die forging process. Itgenerally comes in the form of cylinders resulting from open-die forging.
These open-die forging operations, carried out at around 1,000°C for the Ti64 Titanium alloy, are very costly and energy-consuming. The work carried out within the framework of the project consists in revisiting these operations and simplifying them.
Objective
- High-temperature closed-die forging
- The combination or hybridization of closed die-forging with additive manufacturing technologies
- Simplification of the semi-finished product manufacturing process
Demonstrators based on TRL approach
In order to overcome these technological locks as closely as possible to industrial needs.
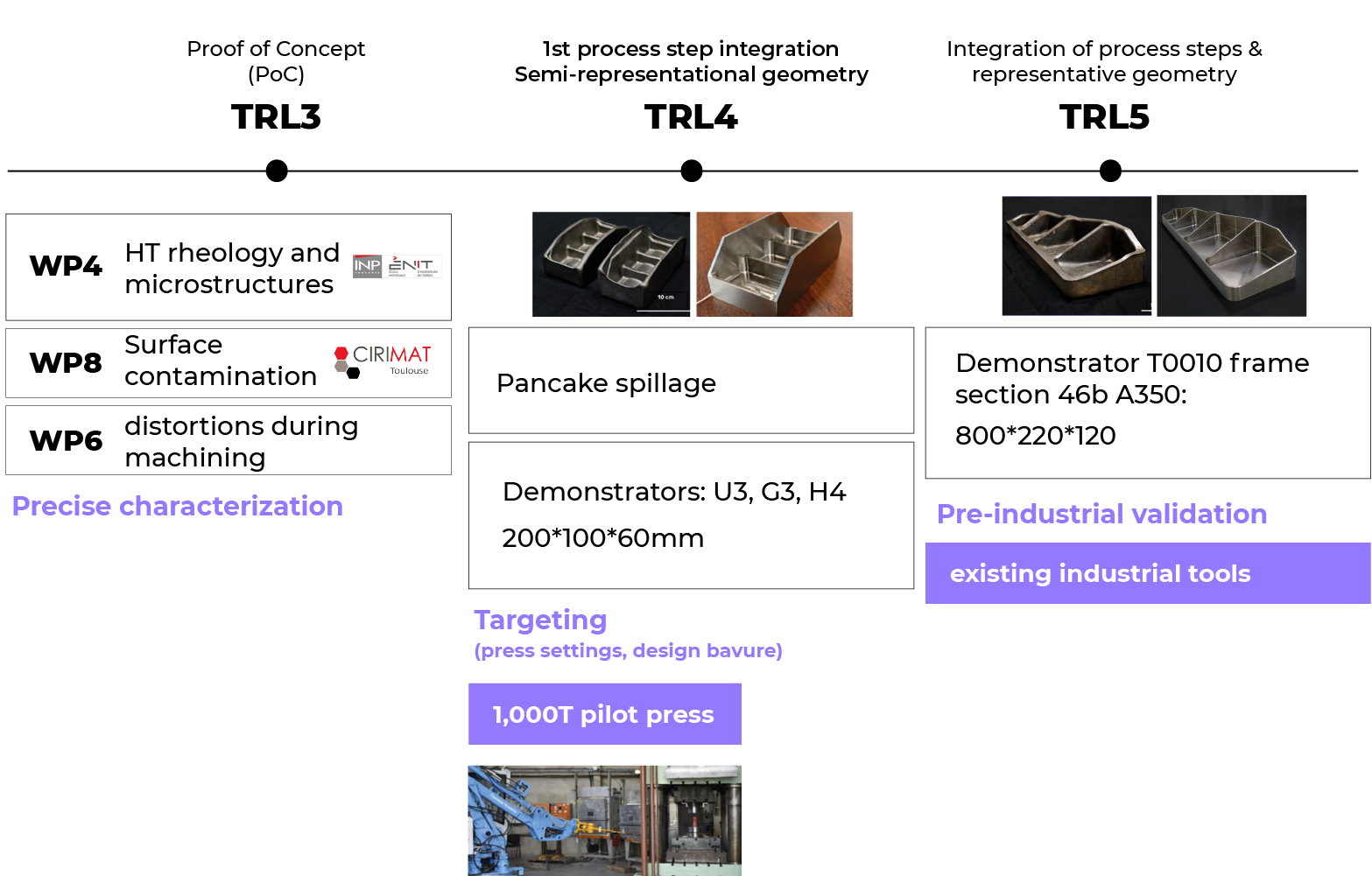
Figure 3 – MAMA project TRL approach
Demonstrator
TRL 5/6 high-temperature closed-die forging demonstrator
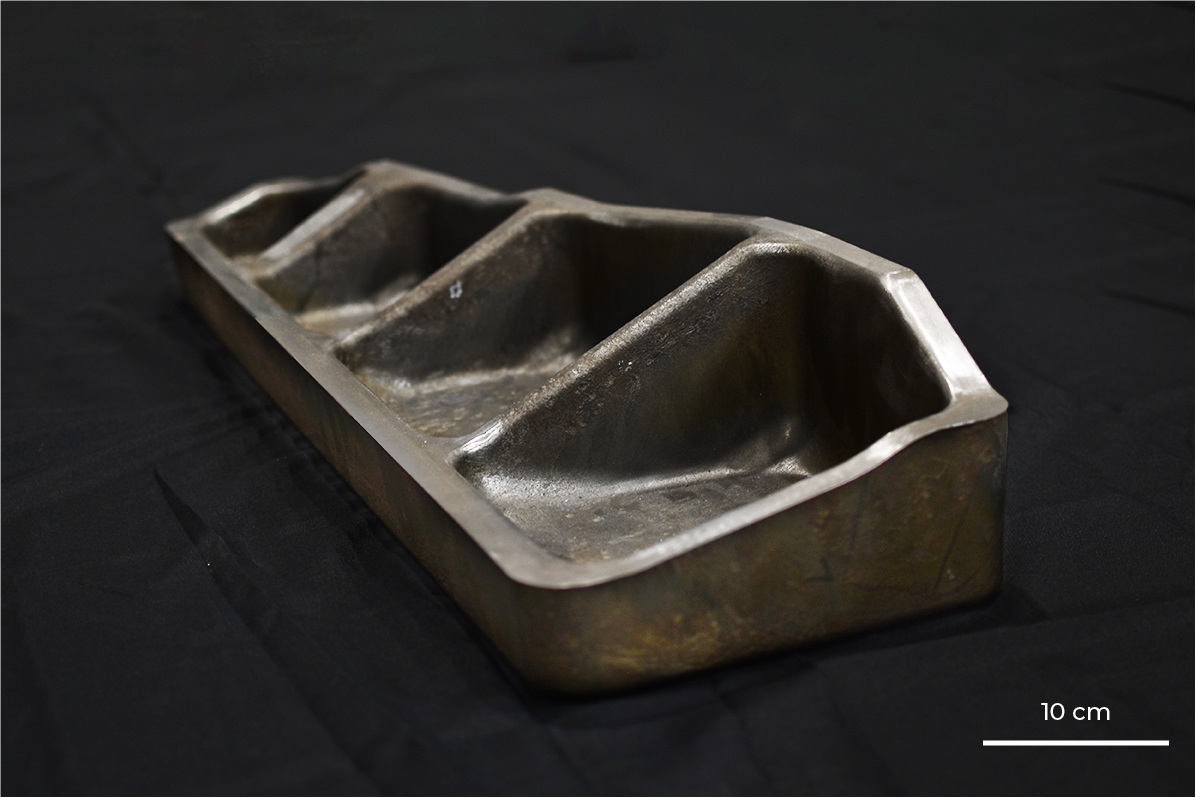
Figure 4 - representative section of an Airbus A350 fuselage frame, TRL 5 & TRL6
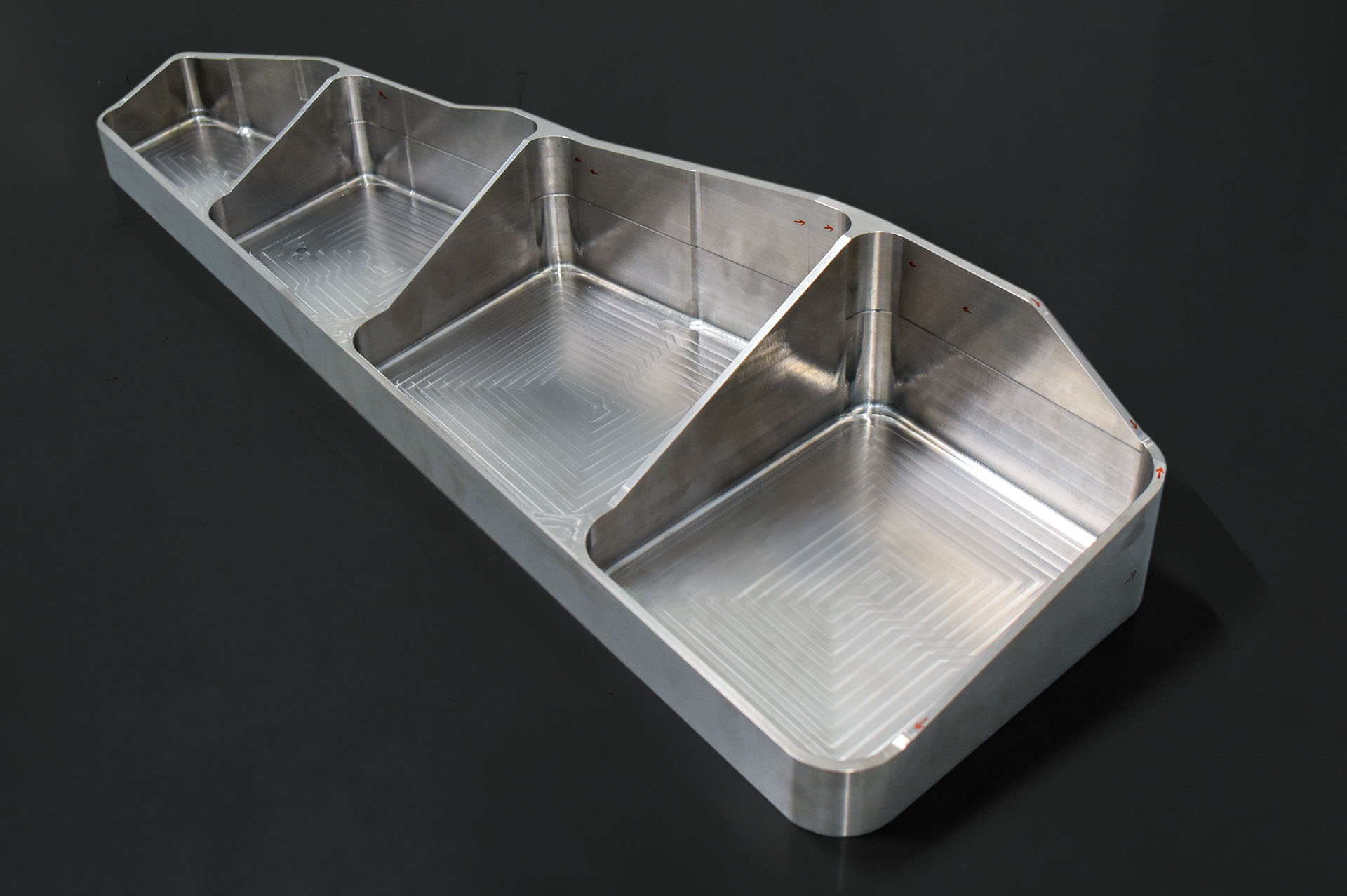
Figure 5 – Same section after finish machining
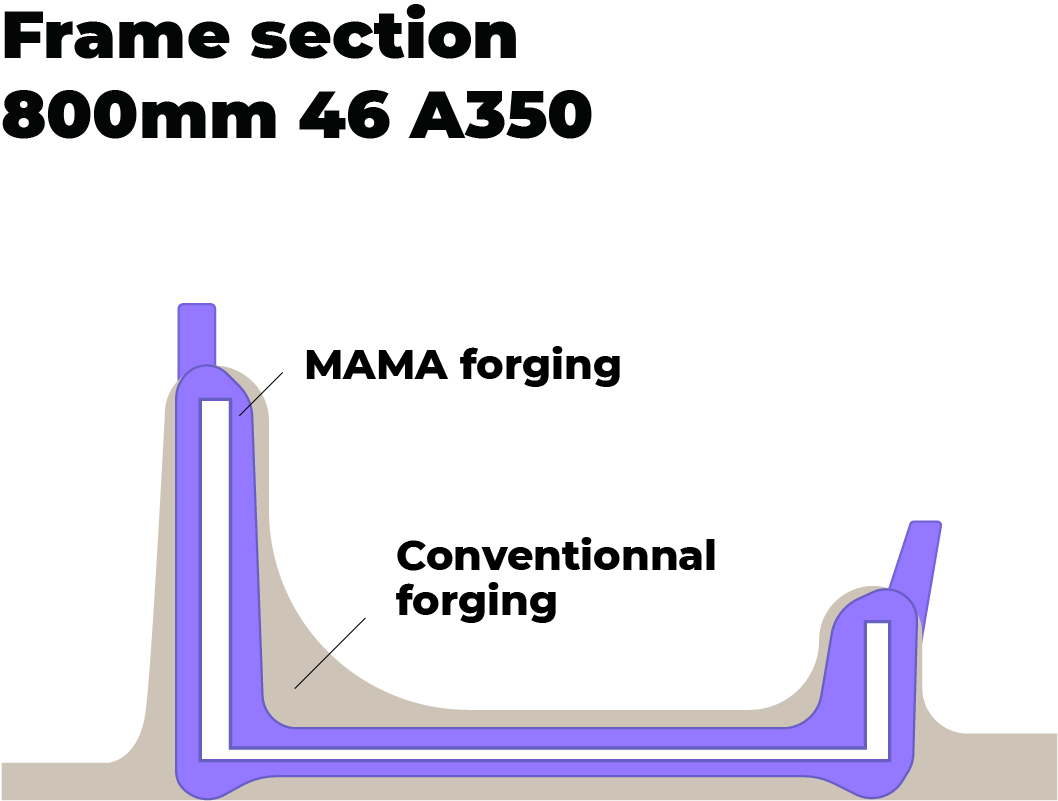
Figure 6 - Principle for reducing the weight of titanium used in closed die-forging
A major change of scale has taken place with a view to validating the TRL5 level (Figure 4) and then the TRL6 level in autumn 2023, on 800 mm long demonstrators corresponding to a representative section of an Airbus A350 fuselage frame.
Manufacturing realism has also progressed considerably, thanks to the introduction of distribution forging prior to closed-die forging and closed-die forging on an industrial press - Aubert & Duval's 22,000-ton press. The other processing stages, hot (heat treatment) and cold (chemical machining, non-destructive testing and mechanical machining), are also carried out on industrial facilities, including that of partner MECAPREC for final machining (Figure 5).
To demonstrate the added value of high-temperature forging, two slices were cut transversely from forged blanks of fuselage frame parts:
- A closed-die forging part from the process developed within the MAMA framework with very high-temperature closed-die forging - Figure 6
- A closed-die forging part from the conventional process used by Aubert & Duval, retained for series production before the MAMA research - Figure 6
Results of the MAMA project
high-impact results for the industry and a future project scheduled for November 2023!
With a total of 8 closed-die forged demonstrators, all of which, after chemical machining, meet the requirements of dye penetrant inspection and dimensional control, and confirmation that the buy-to-fly ratio has been reduced by 30%, the MAMA project offers exciting prospects for the aerospace industry.
Other A350 fuselage frame demonstrators are currently being manufactured to validate TRL6. This would pave the way for industrialization of the process by AIRBUS, AUBERT & DUVAL and MECAPREC.
The project
MEMBERS
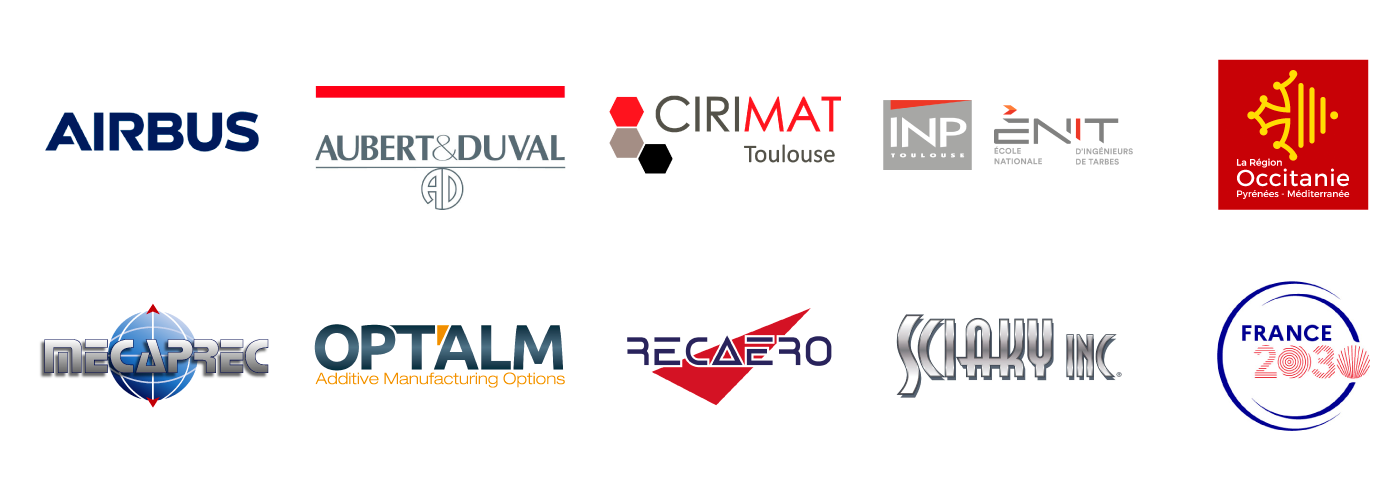